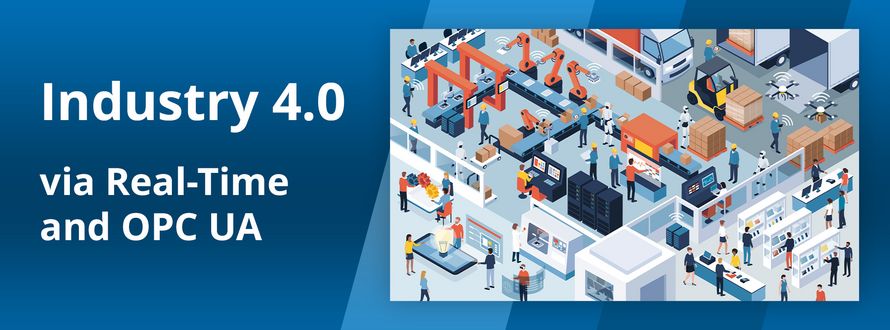
Industry 4.0 via Real-Time and OPC UA
– PikeOS, Industrial Automation, IoTThe OPC UA (Unified Architecture) industrial communication standard has existed for almost twenty years and has since advanced large parts of industry in terms of digitalization. As an important, technological building block, OPC UA enables secure communication within industrial plants, without which Industry 4.0 would be hard to imagine. OPC UA is open, platform-independent and based on a server-client model. It is designed in such a way that every relevant data point can be networked with each other - from small controllers to enterprise servers - and thus enables operational technology (OT) and information technology (IT) to grow together. In addition, the communication standard offers the possibility of remote access to plants, machines, sensor data and agglomerated information. So what added value can SMEs, which have so far shied away from adapting OPC UA, derive from it?
The current Situation
First of all, the need for on-site engineers and technicians will not disappear. However, there is an opportunity to increase efficiency and access to operational data through the use of the latest advancements in technology. Until now, many mechanical engineers have shied away from the use of information technology in their plants. Unfortunately, reservations about software is still widespread. Two things play a major role here: On the one hand, networking is not necessarily trivial and the decision to drive forward the company's own digitization is often one at management level. Many engineers are so busy with their work that optional projects that are not considered mission-critical are pushed aside. But the potential benefits are overlooked: Once networked systems are running at key data points, you get the ability to plan ahead, maintain remotely, and perhaps most importantly: increase overall equipment effectiveness (OEE) by making smart use of the data that accumulates.
What could be possible
Sure: If you know that a C-part component, for example, has a service life of 100,000 operating hours and you plan conscientiously, your equipment will not stand still, or will stand still very little. However, not every servo motor and every vibratory drive adheres to its promised life expectancy. What if a corresponding component could report its status in time? By networking with the ERP system, an order could be automatically flagged, which could be purchased in time and at a cost-effective time. The first providers on the market offer such solutions and help procurement and supply chain managers with plannable information, but above all with valuable time. Few things are more costly than a production stoppage with a simultaneous component shortage, and especially nowadays with highly stressed supply chains where only uncertainty seems to hold, information and time are becoming increasingly important resources.
Of course, it is not always necessary to assume the worst-case scenarios: OPC UA also enables remote operation and maintenance that previously would have required mandatory on-site work. This is a plus for the flexibility of companies and employees, and helps to alleviate personnel bottlenecks or save man-hours in potentially problematic situations. In addition, OPC UA makes it possible to use the information generated to operate plants more effectively and with greater foresight. For example, energy-intensive but time-independent processes could be run when the in-house PV system reports strong solar radiation. In times of expensive energy, smart use of energy is a competitive advantage. In addition to these considerations, however, the greatest role is probably played by the fact that plant operators use the agglomerating information to make their processes more efficient, to discover automation potential that was previously hidden, and to reduce costs and improve processes in the long term.
Secure Communication
Digital information flow used to mean, and to some extent still means, unencrypted data transmission in production facilities. In times when the costs and the numbers of hacker attacks on the industry are exploding, the use of unencrypted data being sent is an extreme risk. OPC UA therefore offers encrypted communication by default. Protocols such as MQTT also offer this, but have the disadvantage that the structure of the data payload is not standardized, therefore the sharing of meta information across multiple devices requires significant additional orchestration to ensure compatibility. If one wants to make a comparison at all, one can say that the use of OPC UA makes it possible to understand a machine more precisely from the outside. In the meantime, so-called Companion Specifications are becoming established, which are used to address comparable machines and system parts, such as presses, in the same way regardless of the manufacturer. This enables greater flexibility through modularity, because a larger selection of machines can now be implemented more quickly.
Use of OPC UA with a Real-Time Operating System
The use of OPC UA with a real-time operating system such as PikeOS makes sense above all at the field level and serves as the basis for offering essential functionalities out-of-the-box that would first have to be programmed bare-metal. A safe and secure system like PikeOS, which separates resources in time and space and guarantees deteministic behavior of data processing such as actuator response or sensor readout, is thus a good basis to enable functionally safe programming of applications that need to work reliably and where failure is not an option. With an appropriate third-party solution, a PikeOS partition can be used to run a securely separated temperature monitoring and control system, for example, while an OPC UA client securely transmits monitoring data to a central OPC UA server in parallel.
The advantage of this connection is that PikeOS is pre-certified against many industrial safety standards such as IEC 61508 and at the same time the version 5.1.3 of the PikeOS Separation Kernel holds the high EAL level 5+ against cybersecurity standard the Common Criteria. This allows functionally safe and cybersecure applications to run - from no controller to full-blown System-on-Chip (SoC). The result is increased safety and security in terms of functionality, data and protection against hacker attacks, as well as a data basis on which effectiveness and efficiency can be increased and costs can be saved while ensuring the greatest possible user-friendliness.
In addition, the use of Time-Sensitive Networking (TSN) offers the possibility of hard, distributed real-time capability. This communication works through a publisher-subscriber model that does not require acknowledgments. The basis for this is the increased performance of industrial Ethernet. This is achieved via the integration of an appropriate stack such as Open62541.
Use Cases
There are many applications of real-time operating systems like PikeOS and OPC UA in industrial automation, such as automotive manufacturing, power generation, aerospace, and medical. Real-time operating systems and OPC UA are important technologies that support the development of intelligent automation systems and enable the future of industrial automation. An example of the use of PikeOS in conjunction with OPC UA is in automotive manufacturing. Here, PikeOS can be used to enable real-time control and monitoring of production processes. By using OPC UA, different systems and devices, such as machines, sensors and controllers, can communicate with each other and exchange data. This makes it possible to monitor and adjust production in real time to improve production efficiency and quality.
It also makes sense for power generation in power plants when turbines, generators and sensors exchange data. Power plant performance and efficiency can be monitored and adjusted in real time. This is particularly interesting for residual load detectors such as coal-fired power plants, as long as renewable energy feeds fluctuate. Tidal power plants and wind farms, of course, also benefit from flexible adaptation to environmental conditions or communication with each other as needed for virtual power plants. The use cases extend across all industries. The basis for digitization exists and can already be used - it just needs to be wanted and implemented.
Out-of-the-Box Solution
SYSGO and Systerel have collaborated to create a joint solution (read the Press Release) for the use of OPC UA. The result: the functionally safe and cyber-secure solution S2OPC can now run natively, i.e. without a guest operating system, on a PikeOS instance. This offers several advantages at once, as it keeps hardware requirements low and resource consumption at a low level. In addition, the integrated solution offers the secure and reliable possibility to implement the OPC UA standard quickly. S2OPC, similar to PikeOS, was created for cyber-secure and functionally safe deployment in the embedded system environment for devices that require real-time capability. As a consequence, the common real-time solution is safety and security certifiable, which is unique in the market and allows system manufacturers to build reliable applications.
More information at www.sysgo.com/pikeos
-
Previous
-
Next